Understanding the Fundamentals and Applications of Plastic Extrusion in Modern Manufacturing
In the realm of contemporary manufacturing, the technique of plastic extrusion plays a crucial duty - plastic extrusion. This detailed procedure, including the melting and shaping of plastic via specialized passes away, is leveraged throughout numerous sectors for the development of varied items. From auto parts to customer products packaging, the applications are huge, and the capacity for sustainability is similarly excellent. Unraveling the fundamentals of this process exposes real adaptability and possibility of plastic extrusion.
The Fundamentals of Plastic Extrusion Process
While it may appear complicated, the basics of the plastic extrusion procedure are based on relatively uncomplicated concepts. It is a production procedure wherein plastic is thawed and after that formed into a continuous profile via a die. The plastic extrusion procedure is extensively used in numerous markets due to its adaptability, cost-effectiveness, and performance.
Different Sorts Of Plastic Extrusion Techniques
Building upon the standard understanding of the plastic extrusion procedure, it is required to explore the various strategies involved in this manufacturing approach. The two key methods are profile extrusion and sheet extrusion. In profile extrusion, plastic is thawed and formed right into a continuous account, frequently utilized to develop pipelines, poles, rails, and window structures. In contrast, sheet extrusion produces big, flat sheets of plastic, which are commonly further refined right into products such as food packaging, shower curtains, and automobile components. Each method calls for specialized machinery and accurate control over temperature level and stress to guarantee the plastic keeps its form throughout air conditioning. Recognizing these techniques is essential to making use of plastic extrusion efficiently in modern-day manufacturing.

The Function of Plastic Extrusion in the Automotive Sector
An overwhelming majority of parts in contemporary vehicles are products of the plastic extrusion process. Plastic extrusion is primarily utilized in the production of various auto components such as bumpers, grills, door panels, and control panel trim. Thus, plastic extrusion plays a pivotal duty in automotive manufacturing.
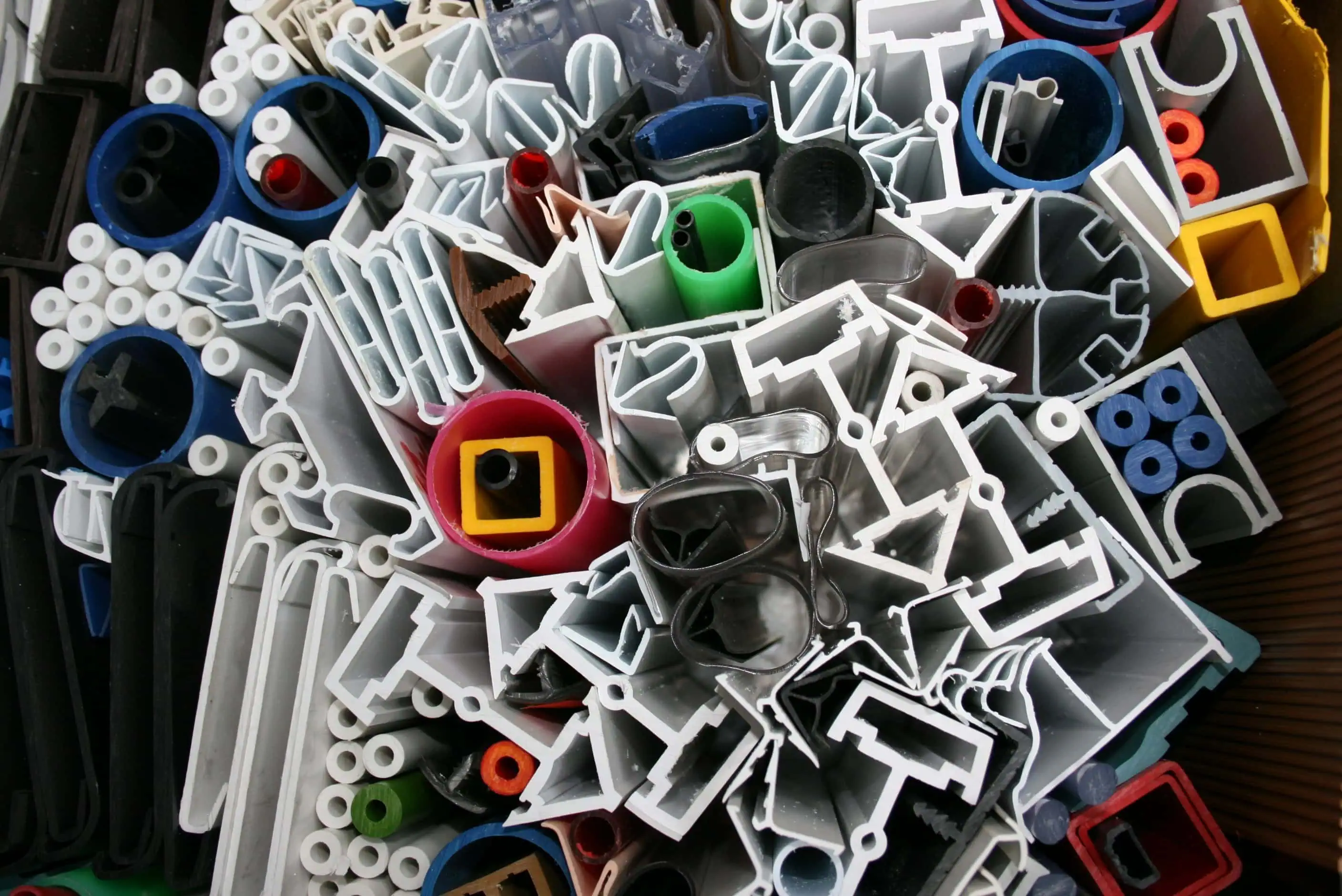
Applications of Plastic Extrusion in Durable Goods Production
Beyond its significant influence on the auto market, plastic extrusion shows just as effective in the realm of consumer important link items making. The convenience of plastic extrusion enables suppliers to create and generate intricate forms and sizes with high precision and performance. The flexibility, adaptability, and cost-effectiveness of check that plastic extrusion make it a favored choice for numerous customer products makers, contributing significantly to the market's growth and technology.
Environmental Effect and Sustainability in Plastic Extrusion
The pervasive usage of plastic extrusion in making invites analysis of its environmental ramifications. As a procedure that regularly uses non-biodegradable materials, the environmental influence can be considerable. Energy intake, waste production, and carbon exhausts are all issues. Nonetheless, market improvements are boosting sustainability. Efficient equipment minimizes power use, while waste administration systems reuse scrap plastic, decreasing resources needs. In addition, the advancement of naturally degradable plastics supplies a much more eco friendly option. In spite of these improvements, better advancement is needed to mitigate the environmental impact of plastic extrusion. As culture leans towards sustainability, makers need to adapt to remain feasible, highlighting the significance of continuous research and advancement in this area.
Final thought
Finally, plastic extrusion plays an essential role in contemporary production, specifically in the auto and consumer goods markets. Its adaptability allows for the manufacturing of useful source a variety of elements with high precision. In addition, its potential for reusing and growth of eco-friendly materials supplies a promising method in the direction of sustainable methods, consequently dealing with environmental issues. Understanding the basics of this procedure is essential to optimizing its applications and benefits.

The plastic extrusion process is thoroughly made use of in different sectors due to its efficiency, flexibility, and cost-effectiveness.
Building upon the basic understanding of the plastic extrusion procedure, it is essential to check out the various methods included in this production technique. plastic extrusion. In contrast, sheet extrusion produces large, flat sheets of plastic, which are typically additional refined right into items such as food packaging, shower curtains, and auto parts.A frustrating majority of parts in modern-day lorries are products of the plastic extrusion procedure